The Hive
WOLFGANG BUTTRESS
Milan Expo 2015
With a relatively small and restricted construction site, a timeline of just twelve months and The Hive alone comprising 169,300 individual components, this was an extremely complex project, but one which played to our strengths and experience.
The pavilion site was a long, thin plot that was divided into a series of zones that culminated with the dynamic Hive structure. Visitors begin their journey walking through an orchard to a ‘swarm wall’ where digital content was shown on over a hundred screens. The pathway then continued through a raised wildflower meadow, allowing an unusual bees-eye perspective of the planting, before they approached The Hive structure.
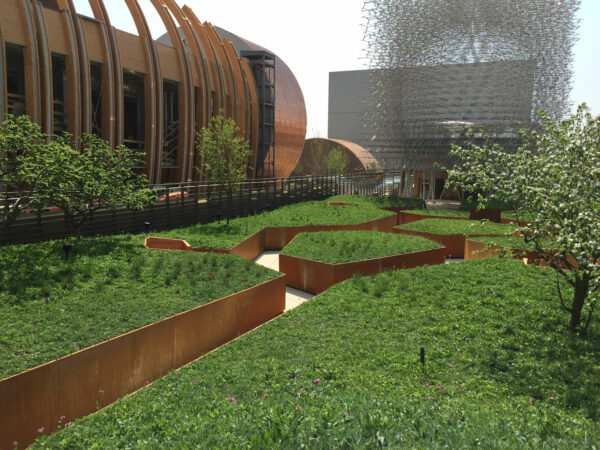
The raised meadow was created by laying tonnes of topsoil on top of staging decks raised on scaffold legs to fulfil the eye-level criteria and reduce the volume of materials needed on site.
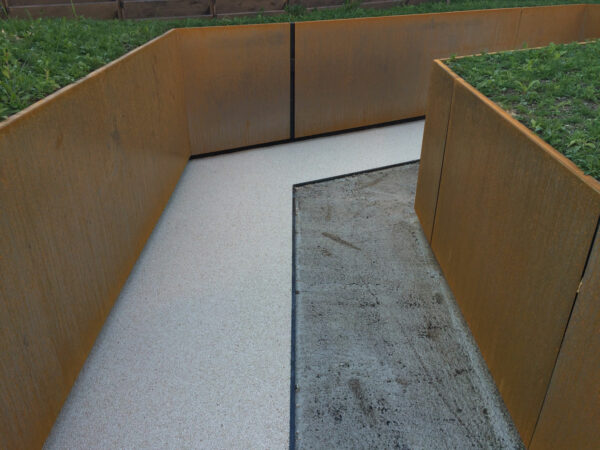
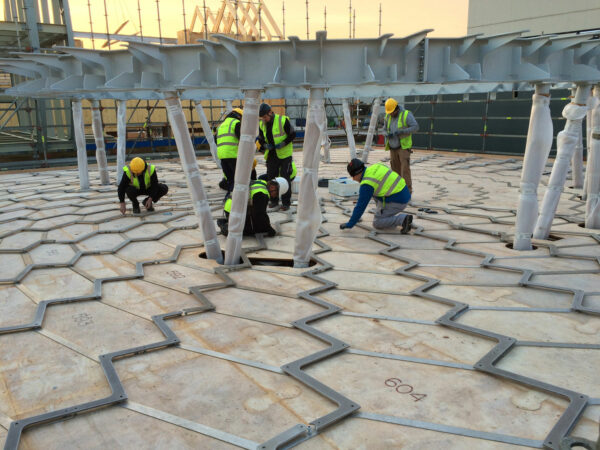
The paths were geometrically designed, referencing the hexagonal cells of The Hive. Cor-ten steel was selected for the retaining walls of the paths as well as the external walls of the hospitality block. A series of 2.3 metre high wooden louvres were manufactured in our wood workshops. These were stained and finished with graphics before being installed along the site perimeter, behind rows of native lavender bushes.
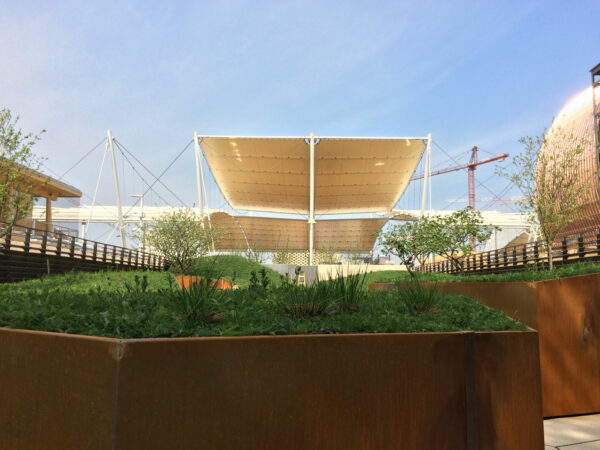
In addition to the pavilion, the work in Milan included end-to-end production and fit out of the hospitality block, an events space, control rooms and a kitchen.
The manufacturing processes kept our machine shop occupied for more than 16 hours a day for five months
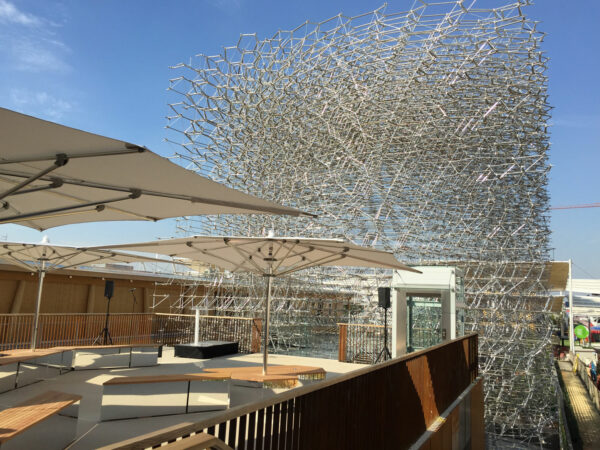
The Hive, Kew Gardens
Effectively, The Hive is a giant truss. Eighteen steel columns were bolted to a concrete pad foundation and supported a 10.8 metre steel ring beam.
Each layer consists of rods and cords of differing length, forming a cuboid structure. The team performed rigorous structural analysis to optimise each of the chords and rods to ensure the structure can hold its own weight.
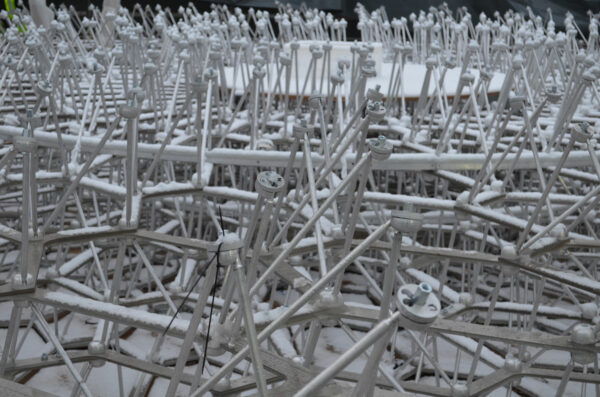
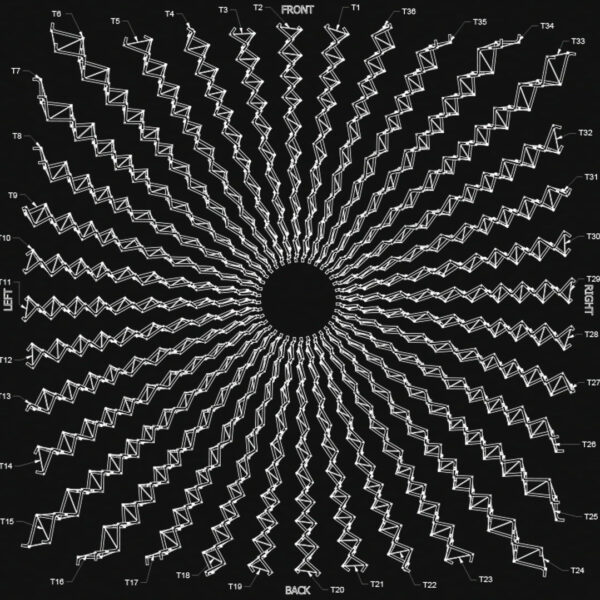
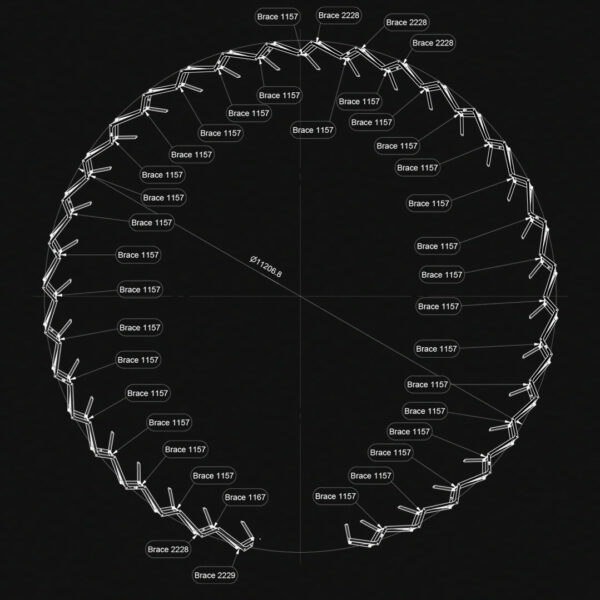
The Hive was designed and manufactured so each component could be bolted together on-site and built up layer-by-layer as a kit of parts. To support the 12-strong on site crew build, de-rig and reinstall the project, the team inscribed the 169,300 parts with a unique number indicating their precise location within the structure.
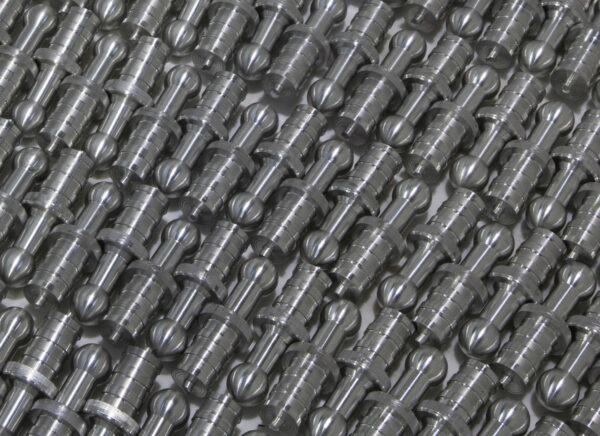
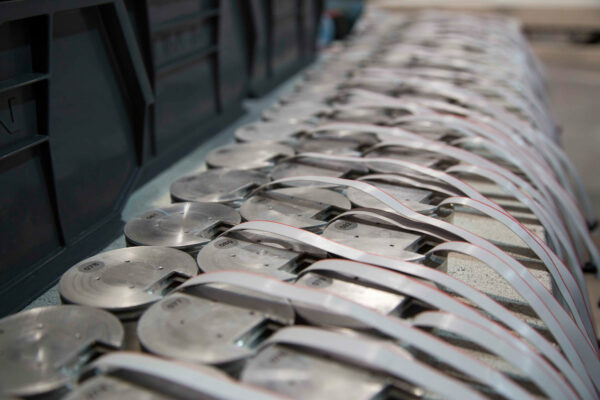
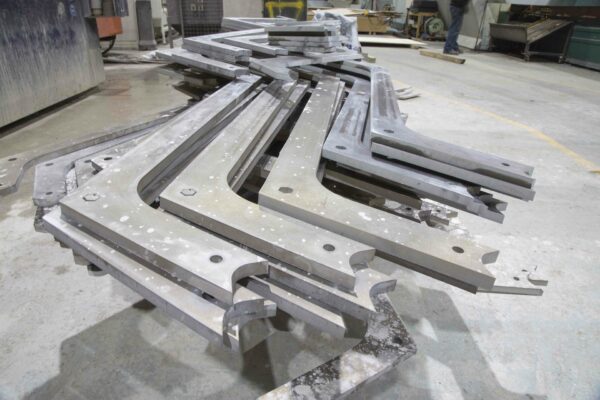
Within the cuboid, there’s an internal spherical void 9 metres in diameter to allow visitors to enter the core of The Hive, where audio and LED lighting hum and pulsate in direct response to a beehive in Kew Gardens. A glass floor gives visitors an unimpeded 360° view of the hexagonal structure that surrounds them, and provides a unique perspective from which to experience the swarm simulation.
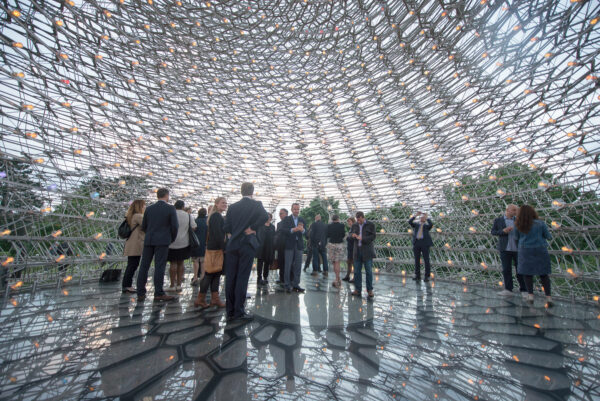
Light sources within The Hive simulate activity captured via accelerometers located within beehives in Kew Gardens. We designed, prototyped, refined and manufactured a custom high power LED light source and control system, made from 1,000 four-colour (RGBW) ‘pixels’ bright enough to be seen in daylight. The array of pixels defines the spherical void and lattice design makes the effects visible from inside and out.
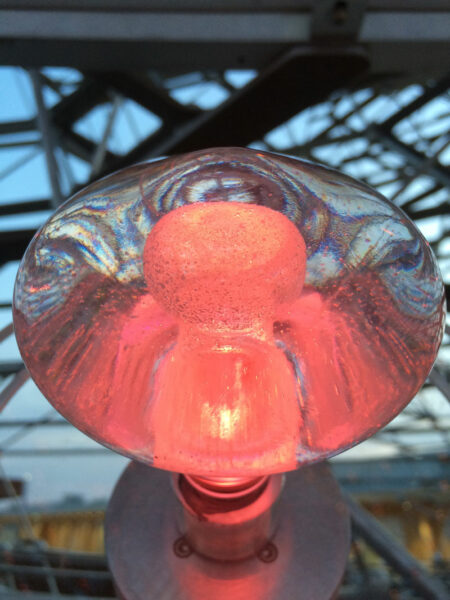
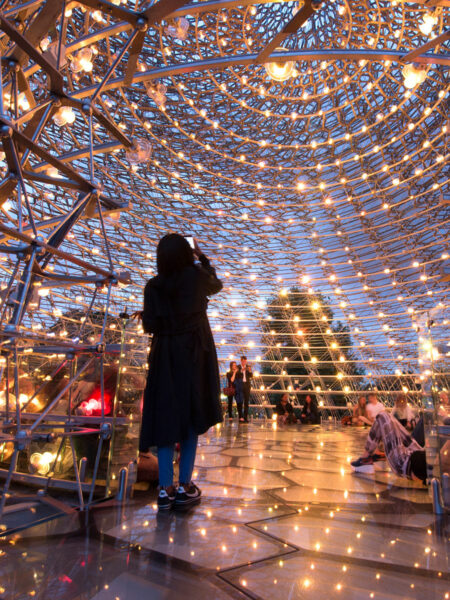
Our electrical engineers worked on the lighting infrastructure and control software, to allow each of the thousand lights to be controlled individually and/or collectively. This included manufacturing the circuit boards, diffusers, housings and heatsinks. Using real time 3D visualisations of the many lighting effects saved a great deal of time once on site.
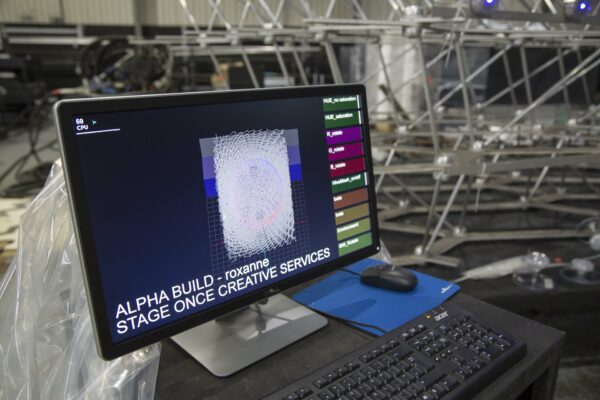
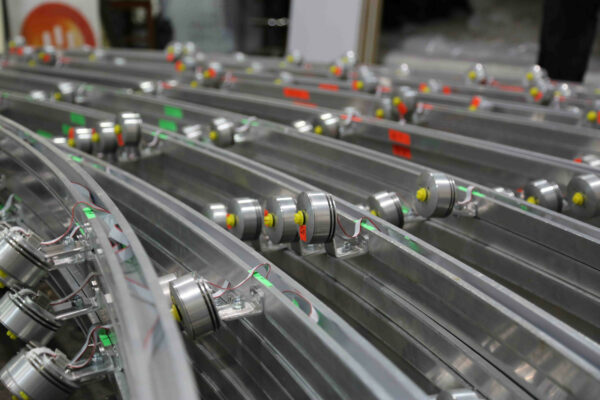
When Expo 2016 was complete, the towering sculpture was de-rigged and re-built at Kew Gardens, London.
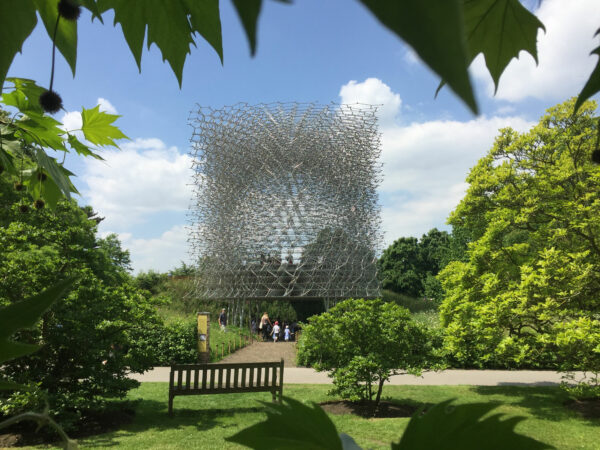
We are truly delighted to announce The Hive’s move to Kew, both for its magnificent aesthetic appeal and for the resonance it has with our work – I can think of no better home for this remarkable marriage of architecture and science.Richard Deverell
Director of the Royal Botanic Gardens, Kew
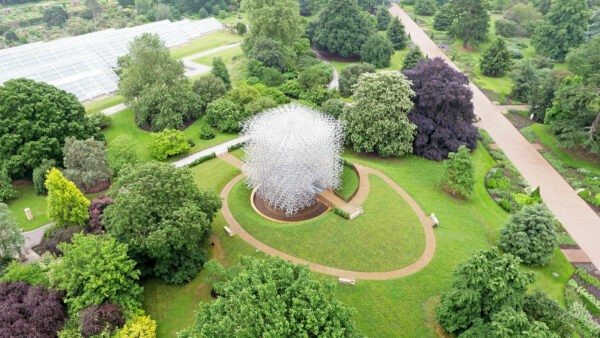
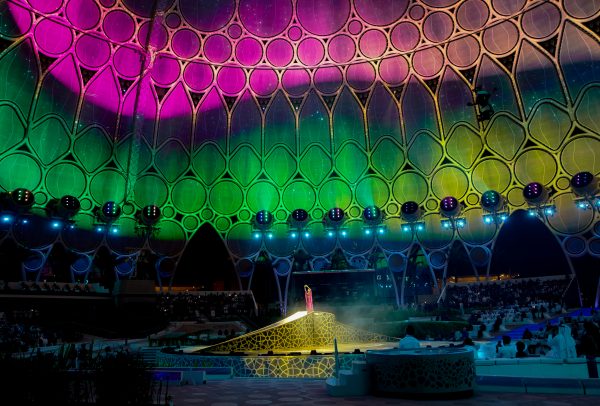